Construction Industry Pipeline inspection is important for ensure the safe, stable and long-term operation of the pipeline system. By different inspection technologies, inspector can discover potential quality problems, Avoid security risks, and improve the service life and function of the pipeline system.
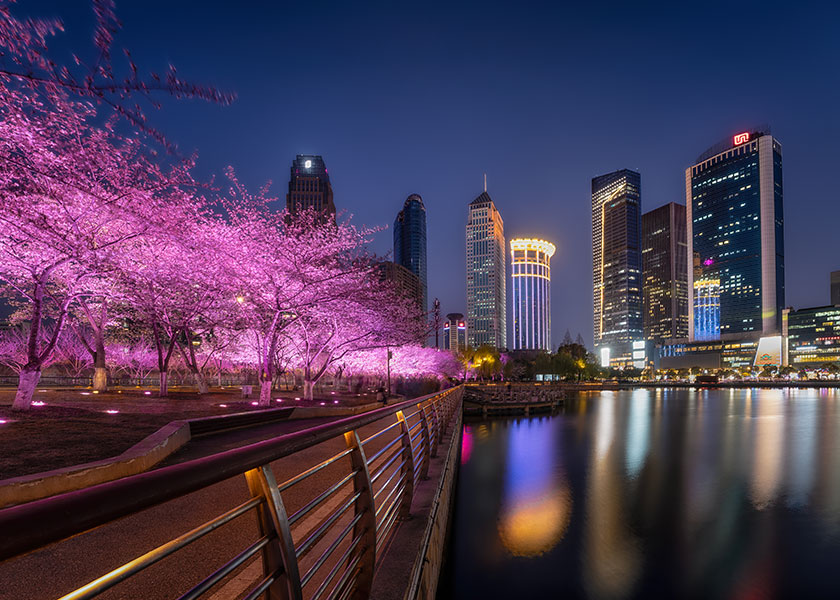
Common pipeline quality inspection and testing methods:
- Visual inspection:
Method: Check the outside the pipe with the our eyes. or with the help of magnifying glasses, hand-held mirrors to find problems such as cracks, deformation, corrosion, and welding quality.
Significance: Simply and quickly find obvious defects on the surface of the pipeline as a basis for further inspections.
- Ultrasonic inspection:
Method: Use ultrasonic probes to transmit sound waves through the pipeline wall. The changes of reflected waves can determine the wall thickness and material defects of the pipeline.
Significance: It can NDT the pipeline inner and outer walls, which is suitable for measuring thickness, identifying defects. such as corrosion and cracks, and ensuring the safety of the pipeline structure.
- X-ray detection:
Method: Use X-rays to penetrate the pipeline and welding area to form an image. analyze the defects. Such as pores, cracks, and poor welding.
Significance: Provides more accurate test results, especially for high-risk pipeline systems. Such as oil and gas pipelines, and can effectively avoid leakage and explosion caused by welding quality problems
- CCTV inspection camera:
Method: Use high-definition pipe inspection camera or a CCTV crawler to enter the Construction Industry Pipeline inspection. take real-time photos of the conditions inside the pipeline, such as cracks, blockages, sediments, corrosion. It generally supports real-time inspection report system.
Significance: Directly see the actual situation inside the pipeline, which is convenient for discovering hidden damage, water accumulation, Blockage and other problems, especially suitable for the inspection of sewer pipe or underground pipelines network.
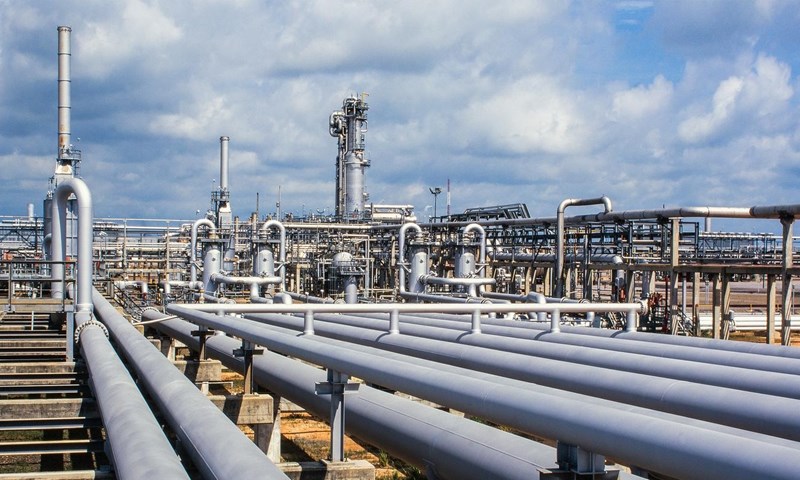
- Pressure inspection:
Method: Fill the air or water into pipeline system inner, inspect the sealing of the pipeline, and check whether there is leakage.
Significance: Ensure the pressure bearing capacity and sealing performance of the pipeline system in actual use, and avoid pipeline leakage cause safety accidents.
- Penetration detection:
Method: Use penetrant to check for tiny cracks or defects on the surface of the pipeline, especially for metal pipelines.
Significance: Can detecte very fine cracks on the surface to ensure the integrity of the pipeline surface.
- Magnetic particle inspection:
Method: By sprinkling magnetic powder on the surface of ferromagnetic materials, the magnetic field is used to display the defective parts and detect surface or near-surface cracks.
Significance: Suitable for the detection of welding parts and surface cracks, especially the quality inspection of steel pipelines.
- Air tightness detection:
Method: Detect whether there is a gas leakage problem in the pipeline, which is very important in the inspection of gas pipelines.
Significance: Ensure that the pipeline will not leak during actual use, and avoid dangerous accidents such as fire and explosion caused by gas leakage.
The significance of Construction Industry Pipeline inspection
Ensure safety:
As an important part of construction projects, pipelines involve the transmission of liquids and gases. Any quality problems may cause serious safety accidents. Such as gas leakage explosion, water pollution, etc. Through systematic detection, hidden dangers can be discovered in advance to avoid accidents.
Improve the service life of the pipeline system:
Regular pipeline quality inspection can timely inspect aging, corrosion, wear and other problems, repair and maintain them, extend the service life of the pipeline, and reduce greater losses caused by aging.
Ensure construction quality:
During the pipeline construction process, strict quality inspection can ensure that the construction process is implemented in place, avoid quality problems caused by improper construction, and ensure that the final project meets the design standards and safety requirements.
Save maintenance costs:
Regular pipeline inspection can identify small-scale problems in time and avoid large-scale damage. Early inspection and maintenance can reduce sudden overhauls and reduce long-term operating costs.
Comply with regulations and standards:
The quality standards and regulations for construction projects in various countries or regions have clear provisions for pipeline quality inspection. Through these inspections, it can be ensured that the project complies with the regulations and avoid legal liabilities and additional economic losses caused by non-compliance.
Improve the operational efficiency of pipelines:
Enhance customer trust and market competitiveness:
For construction engineering companies, high-quality construction Industry Pipeline inspection can enhance the company's reputation, enhance customer trust, and help gain a competitive advantage in the market.
Overall, pipeline quality inspection and testing in construction projects is not only the basis for ensuring construction quality and safety, but also essential for later maintenance and operation management. Use NDT technology can improve the reliability and stability of the pipeline system, thus reduce potential risks.