Urban Underground Comprehensive Pipeline Gallery are a critical part of modern city infrastructure. These underground comprehensive pipeline gallery accommodate various utility facilities systems such as water supply lines, sewerage, electrical cables, gas pipelines, telecommunication networks, and other essential services. The development and maintenance of these underground comprehensive pipeline gallery require detail planning, construction techniques, and ongoing management to ensure their efficiency, safety, and longevity.
Inspecting an underground comprehensive pipeline gallery is a critical process to ensure the safety, integrity, and efficiency of the entire utility facilities system. These inspections help inspect issues like leakages, structural damage, corrosion, blockages, or signs of wear before they escalate into more serious problems. Here's a detailed guide on how to inspect an underground comprehensive pipeline gallery:
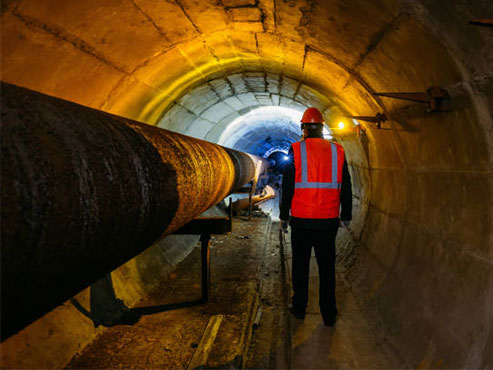
1. Inspection Preparation
- Safety Precautions: Ensure all safety protocols are in place before conducting an inspection. This includes ensuring the gallery is safe for entry, providing personal protective equipment (PPE) for inspectors, and establishing ventilation if need.
- Gather Equipment: Depending on the scope of the inspection, need the following tools and equipment:
- CCTV inspection cameras (for pipe inspection)
- Robotic crawlers camera (for remote inspections)
- Gas detectors (to check for harmful gases)
- Thermal imaging cameras (to detect temperature variations)
- Ultrasonic thickness gauges (to measure pipe wall thickness)
- Inspection drones (for surveying hard-to-reach areas)
- Inspection logs and documentation systems
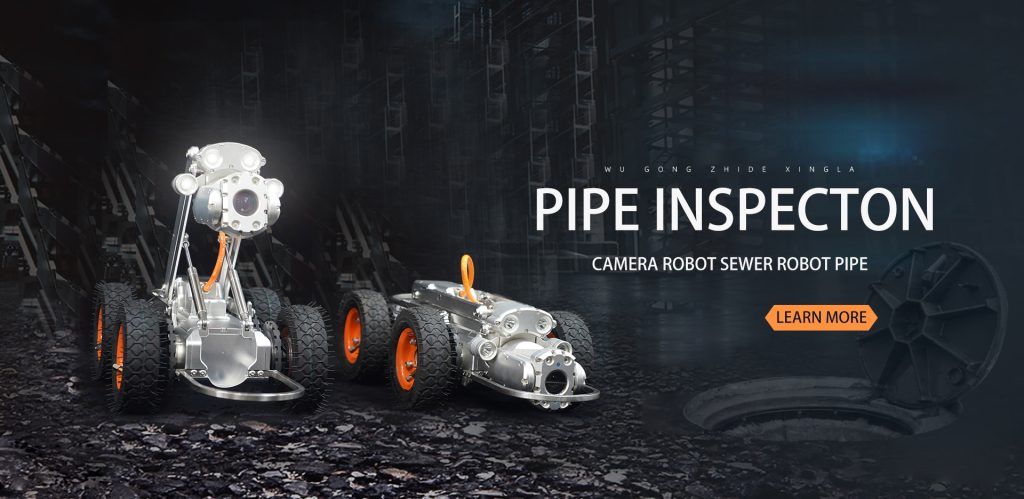
2. Visual Inspection
- Access Points: First, inspect the entry/exit points and ventilation shafts to ensure they are intact and accessible. Check for signs of leakage, structural damage, or any obstructions that might prevent proper functioning.
- Gallery Walkthrough: If the gallery allows human entry, inspectors should walk through the gallery to visually inspect the condition of the structure. They should look for:
- Cracks, leaks, or signs of water ingress
- Deformation or settlement of walls and floors
- Evidence of rust or corrosion on metallic components
- Obstructions or debris blocking pipes or access paths
- Lighting: Ensure the gallery is adequately lit for inspection, as poor lighting can hinder the identification of problems.
3. Remote and Automated Inspections
- CCTV Pipeline Inspection crawler: For detailed internal pipe inspections, a CCTV camera system can into pipes inner. The inspection camera should be able to capture real-time Photos and Videos, allowing inspectors to:
- Detect cracks, leaks, or corrosion inside the pipes
- Assess the condition of joints and connections
- Identify build-ups of debris, sediment, or biofilm that could obstruct the flow of materials
- Record any signs of misalignment or displacement of pipes
- Pipe Robotic Crawlers: If the pipe diameter and structure allow, robotic crawlers with cameras, sensors, and even cleaning tools can be used to inspect and clean the interior of pipes. These robots can move long distances and provide high-definition images and real-time data to operators.
- Sonar Inspection equipment: Acoustic sensors or listening devices can detect leaks or changes in the pressure within pipes. These devices can identify abnormal sounds that indicate potential issues like cracks, ruptures, or leaks.
4. Non-Destructive Testing (NDT)
Non-destructive testing methods help assess the condition of the pipes and structure without causing damage. Some common NDT methods include:
- Ultrasonic Testing: Ultrasonic thickness gauges are used to measure the thickness of metal pipes to inspect corrosion or wear over time. This can also help detect structural weaknesses that may not be visible on the surface.
- Magnetic Particle Testing: This is used to detect surface or near-surface cracks in ferromagnetic materials. A magnetic field is applied to the pipe’s surface, and iron particles are used to highlight any defects.
- Thermographic (Infrared) Inspection: Infrared cameras can detect temperature variations along the pipe. Hot spots can indicate blockages, leaks, or other anomalies that need further investigation.
5. Environmental Monitoring
- Gas and Chemical Monitoring: Underground galleries can contain hazardous gases like methane, hydrogen sulfide, or carbon monoxide, particularly if there’s a leak or failure. Gas detectors should be used to monitor for any dangerous emissions.
- Water Infiltration and Drainage: Inspect the drainage system for any signs of water ingress, which can weaken the structural integrity of the gallery and the pipes. Leaks or rising groundwater can cause serious issues over time, especially if not detected early.
- Humidity and Temperature Sensors: Monitoring environmental conditions, such as humidity and temperature, can help predict corrosion risks and other degradation in materials.
6. Structural Inspection
- Concrete Inspection: If the gallery has concrete walls, floors, or ceilings, check for cracks, signs of spalling, or any visible structural damage. Concrete may also show signs of chemical degradation from water or gas exposure.
- Structural Load Testing: In certain cases, conducting load tests can help verify the structural integrity of the gallery, especially in areas prone to subsidence or seismic activity.
- Corrosion Inspection: Look for visible signs of corrosion on metallic structures, especially in areas with high moisture content. A detailed inspection with corrosion mapping tools may be required to assess the severity of the corrosion and determine whether repairs or replacements are needed.
7. Documentation and Reporting
- Inspection Logs: Keep detailed records of all inspections, including:
- The areas inspected
- Picture and video
- defect location
- Tools and methods used
- Any abnormalities or issues identified
- Corrective actions recommended or taken
- Photographs and Videos: Capture visual evidence of any issues found during the inspection, which can help during future inspections or in repair planning.
- Condition Indexing: Many pipeline inspection systems use condition indices to rate the overall health of the pipes. These indices can help prioritize repairs based on severity and risk.
8. Post-Inspection Activities
- Repair Recommendations: Based on the findings, generate recommendations for repairs or upgrades. Prioritize actions based on the severity of the issue and its impact on the system’s functionality.
- Cleaning and Maintenance: After inspection, the gallery may need to be cleaned of any debris or build-ups found in the pipes. This helps restore optimal flow and prevents future issues.
- Preventive Measures: Develop a regular maintenance schedule to address minor issues before they become major problems. Use the inspection data to inform future maintenance and monitoring practices.
9. Use of Advanced Technologies
- Drones for Hard-to-Reach Areas: In some cases, drones equipped with cameras and sensors can be used to inspect areas that are difficult to access, such as deep shafts, large chambers, or tunnels.
- AI and Machine Learning: Advanced image analysis and AI-powered tools can assist in identifying problems in video footage, significantly speeding up the process and increasing accuracy in diagnostics.
All in all, By combining these methods, achieving a thorough inspection of an underground comprehensive pipeline gallery, helping to extend the life of the infrastructure and ensure the safe and continuous operation of utility systems.
Would you like more specific information about any particular inspection tool or technique?