In the world of industrial maintenance, Non-Destructive Testing (NDT) is a cornerstone for ensuring the integrity of pipelines, which are vital for transporting resources like oil, gas, and water. Traditional inspection methods, while useful, often fall short in terms of efficiency, safety, and accuracy. Enter pipeline inspection robots—cutting-edge tools that are redefining how we approach NDT. This article explores the transformative impact of these robots on pipeline maintenance, emphasizing their role in boosting safety, efficiency, and accuracy.
The Need for Advanced NDT Solutions in Pipeline Inspection
Non-Destructive Testing encompasses a range of techniques used to assess the condition of materials, components, and structures without causing any harm. In the context of pipeline inspection, NDT is vital for:
- Ensuring Safety: Identifying defects and potential failures before they lead to hazardous situations.
- Maintaining Reliability: Ensuring continuous and efficient operation of pipeline systems.
- Compliance: Meeting regulatory standards and industry requirements.
- Cost Efficiency: Reducing the need for costly repairs and downtime through early detection of issues.
How Pipeline Inspection Cameras and Robots Enhance NDT
Traditional inspection methods often fall short when it comes to reaching inaccessible areas or providing detailed, real-time data. This is where pipeline inspection cameras and robots come into play. These advanced tools are revolutionizing the field of NDT by offering unparalleled access, precision, and efficiency.
1. Access to Hard-to-Reach Areas
One of the significant advantages of using pipeline inspection robots is their ability to navigate through complex and hard-to-reach environments. Whether it’s underwater, underground, or in narrow and winding sections, these robots are designed to travel where human inspectors cannot, ensuring comprehensive coverage and detection of potential issues.
2. High-Resolution Visual Inspection
Equipped with high-resolution cameras and advanced sensors, these robots provide clear visuals and precise data that enable accurate detection of corrosion, cracks, and other defects. The high-definition imaging ensures that even the smallest anomalies are captured, reducing the risk of overlooked issues that could escalate into serious problems.
3. Real-Time Data Collection and Analysis
Modern pipeline inspection robots offer real-time data transmission, allowing for immediate analysis and decision-making. This capability is crucial for addressing potential threats promptly, minimizing downtime, and ensuring continuous operation. Real-time data collection also supports proactive maintenance strategies, preventing minor issues from turning into major failures.
4. Multi-Sensor Integration for Comprehensive NDT
Pipeline inspection robots can be equipped with multiple sensors, such as ultrasonic, magnetic, and eddy current sensors, to conduct various NDT methods simultaneously. This multi-sensor integration enhances the accuracy and reliability of inspections, providing a more complete picture of the pipeline's condition and facilitating informed decision-making.
Integrating multiple sensors into a single device enhances the accuracy and reliability of the inspection, providing a complete assessment of the pipeline's condition.
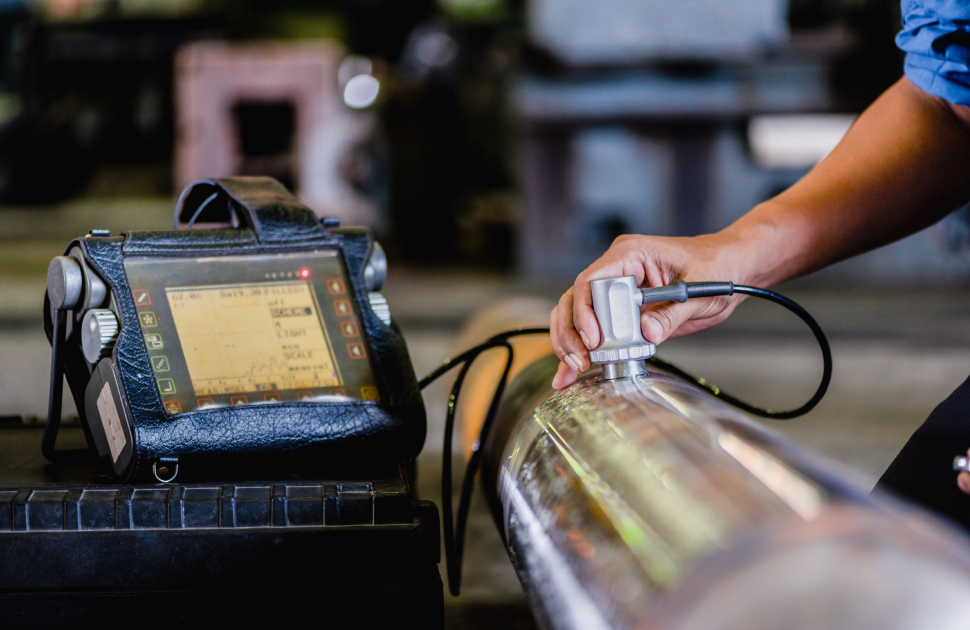
5. Autonomous and Remote Operation
Many inspection robots are designed for autonomous or remote operation. Autonomous robots navigate pipeline systems based on pre-programmed instructions, while remotely operated robots allow human inspectors to control their movements and functions from a safe distance. This feature significantly increases inspection safety by reducing the need for human presence in hazardous environments. Remote operation also allows for real-time inspections, providing immediate feedback and enabling swift action.
6. Data Logging and Analysis
Advanced inspection robots are equipped with data logging capabilities, storing all collected data for later analysis. This historical data is invaluable for tracking the pipeline's condition over time, identifying trends, and predicting future issues. Data logging facilitates proactive maintenance, helping operators address potential problems before they become critical. Analyzing past inspection data also aids in compliance with regulatory requirements and industry standards.
Key Features of Pipeline Inspection Cameras and Robots
To fully grasp the transformative role of pipeline inspection cameras and robots in Non-Destructive Testing (NDT), it's crucial to focus on their advanced features. These tools are engineered with cutting-edge technology, enabling them to expertly navigate intricate pipeline networks. They capture high-resolution images, endure extreme environmental conditions, and generate detailed data for thorough analysis. These attributes are vital for conducting precise and reliable inspections, which are essential for maintaining the safety and operational efficiency of pipeline infrastructure.
1. Mobility and Navigation
Inspection robots are designed to move through complex pipeline systems, including sections with varying diameters, bends, and vertical orientations. They are equipped with traction systems such as tracks, wheels, or caterpillars, allowing them to maneuver smoothly through pipelines. Some models can even climb vertical sections, enhancing their reach and versatility.
2. Lighting Systems
To ensure clear visual inspection, inspection robots are equipped with powerful LED lighting systems. These lights illuminate the pipeline's interior, providing clear visuals even in dark or submerged environments. The lighting systems are robust and durable, capable of withstanding the harsh conditions inside pipelines.
3. Environmental Adaptability
Inspection robots are built to withstand various environmental conditions, including high pressure, extreme temperatures, and underwater environments. Their construction materials are chosen for durability and resistance to corrosion and mechanical damage, ensuring reliable performance in a wide range of conditions.
4. Robust Construction
The robust construction of inspection robots ensures their durability and longevity. They are made from high-quality materials that resist corrosion, mechanical damage, and other forms of wear and tear. This construction ensures that the robots can withstand the rigors of pipeline inspection, providing reliable performance over time.
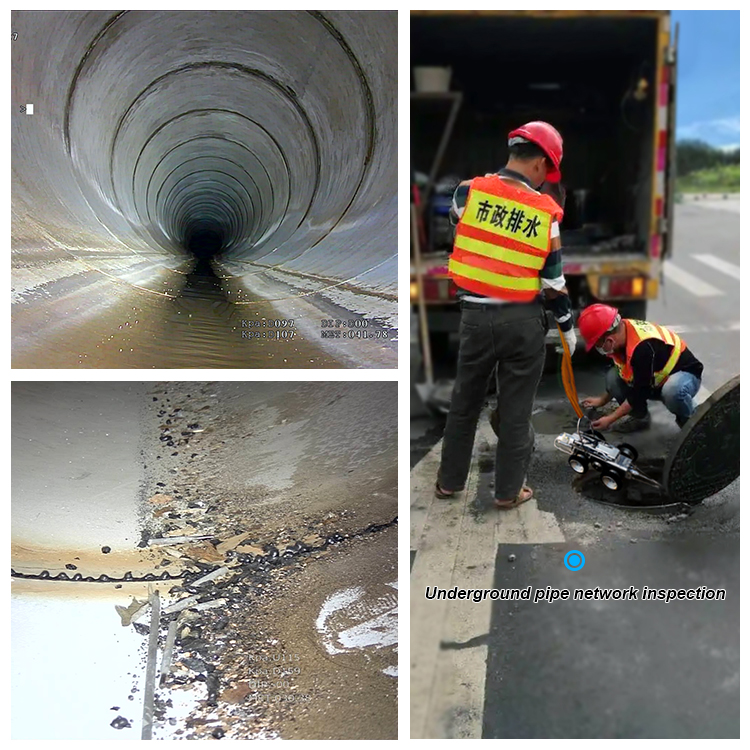
Where Are They Used?
Pipeline inspection cameras and robots are versatile tools employed across a variety of industries to ensure the integrity and safety of critical infrastructure. From oil and gas pipelines that traverse vast and remote areas to water supply systems that deliver essential resources to communities, these advanced inspection technologies play a vital role in maintaining operational reliability. In this section, we will explore the diverse applications of pipeline inspection cameras and robots, showcasing how they are utilized in different sectors to prevent failures, comply with regulatory standards, and promote efficient maintenance practices.
Oil and Gas Pipelines
In the oil and gas industry, the stakes are high, and the need for reliable pipeline inspection is paramount. Robots play a crucial role in detecting and addressing potential issues such as leaks, corrosion, and cracks, ensuring the safe transport of hydrocarbons and compliance with strict industry regulations.
Water Supply Pipelines
Water supply pipelines must be maintained to prevent leaks and ensure water quality. Inspection robots monitor the condition of these pipelines, identifying issues such as corrosion, blockages, and structural damage. Detecting and addressing these issues early prevents water loss, contamination, and costly repairs.
Wastewater Management
Wastewater pipelines are exposed to harsh conditions, including corrosive substances and high levels of biological activity. Inspection robots monitor the condition of these pipelines, detecting issues such as corrosion, cracks, and blockages. Regular inspections ensure the efficient operation of wastewater systems, preventing environmental contamination and health hazards.
Chemical Processing Pipelines
Pipelines used in chemical processing must be maintained to prevent leaks and accidents. Inspection robots detect corrosion, cracks, and other defects that could compromise pipeline safety. Detailed and accurate data from these robots help operators maintain pipeline integrity and comply with safety regulations.
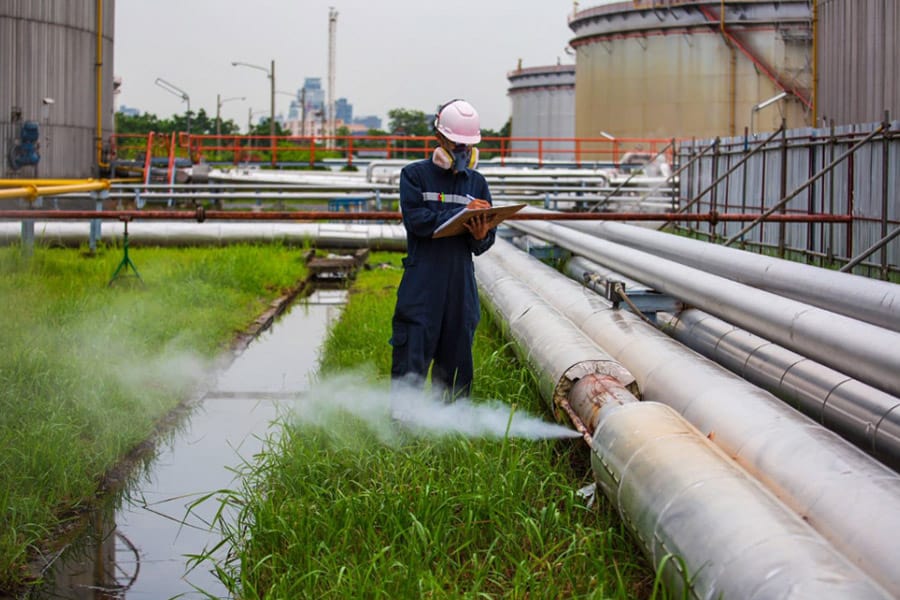
Why Use Inspection Cameras and Robots Rather than Manual Inspection?
While traditional manual inspections have long been a staple in maintaining pipeline integrity, the advent of pipeline inspection cameras and robots has introduced a more efficient and effective alternative. These advanced tools offer several distinct advantages over manual methods, revolutionizing the approach to NDT. In this section, we will examine why using pipeline inspection cameras and robots is superior to manual inspection, highlighting the benefits of enhanced safety, improved accuracy, increased efficiency, and cost savings. Understanding these advantages underscores the value of integrating these cutting-edge technologies into routine pipeline maintenance and inspection programs.
Enhanced Safety
One of the most significant benefits of using inspection robots is the enhanced safety they offer. By reducing the need for human presence in hazardous environments, these robots mitigate the risks associated with manual inspections. Remote operation capabilities further enhance safety by allowing inspectors to control the robots from a safe distance.
Improved Accuracy and Reliability
Inspection robots provide highly accurate and reliable data, thanks to their advanced imaging and sensing technologies. Integrating multiple NDT methods in a single device ensures a comprehensive assessment of the pipeline's condition, reducing the risk of missed defects. High-resolution visuals and detailed sensor data enable precise identification of issues, facilitating timely and effective repairs.
Increased Efficiency and Cost Savings
Inspection robots significantly increase the efficiency of the NDT process. Their ability to quickly navigate pipelines and provide detailed, real-time data reduces the time required for inspections. This increased efficiency translates into cost savings, as it minimizes labor costs, reduces downtime, and prevents costly repairs through early detection.
Conclusion
Pipeline inspection machines have revolutionized Non-Destructive Testing, offering advanced capabilities that enhance the safety, accuracy, and efficiency of pipeline inspections. These technologies provide access to hard-to-reach areas, high-resolution visual inspection, real-time data collection, and multi-sensor integration, making them invaluable tools for maintaining the integrity of critical pipeline infrastructure. By adopting these advanced inspection methods, operators in various industries can ensure the continued safe and reliable operation of their pipeline systems, ultimately protecting the environment and public safety.